Capabilities
Our purpose is to enable our customer’s success through premium engineered solutions. We do this by providing precision manufacturing, design and metrology services that meet our clients’ production needs.
Our machining solutions cater for a wide range of products and projects, from rapid prototyping for R&D projects to scalable volume production of components and assemblies, all with a focus on maintaining quality throughout.
Our continual investment in high-end subtractive manufacturing equipment means we have a diverse range of capabilities that allow us to achieve high accuracy and repeatability even on the most challenging materials. Our advanced machining manufacturing equipment which includes lights-out robotic cells, enables increased capacity, capability and reliability. Combined with our focus on employee upskilling, training and development, it is a winning combination that enables us to add maximum value to our client supply chains.
Design
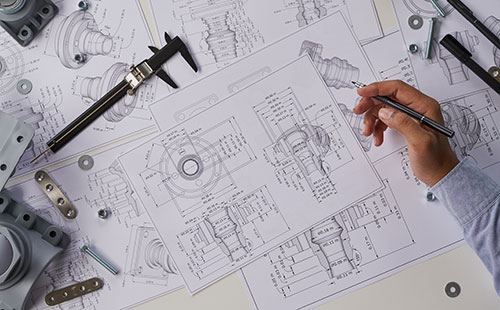
Product Development / Product Design / Process Equipment / DFM (Design for Manufacturability)
Here at Dawnlough our in-house design department has extensive experience delivering complex design solutions to various industries around the world.
Our speciality lies in designing customised process equipment for the medical device industry; however, we have also offered our services to the aerospace industry, marine technology sector, automotive industry and the robotics sector.
Our team of design engineers work closely with each of our customers to bring them complete end-to-end design solutions. With a “Right First Time” approach to each of our designs, we pride ourselves in our ability to take our clients initial ideas, and through rigorous testing and product development, turn them into a reality.
Our design engineers are experts in the use of both Solidworks and Catia V5 through which we provide our 3D CAD/CAM work, while working to the latest drafting and GD&T standards. Our use of CAD/CAM software, together with the extensive manufacturing capabilities at our disposal, provides a seamless transition from design to manufacture.
Our team of engineers also have experience in CE marking equipment that requires compliance under the Machinery Directive 2006/42/EC.
CNC Machining
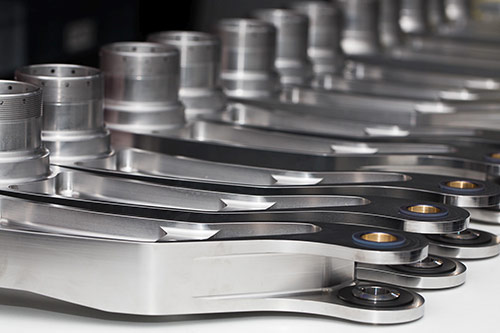
Precision machining has been a core competency of Dawnlough for more than 30 years. We have a comprehensive range of high-end CNC machines capable of producing complex components with intricate geometric and freeform features to very tight tolerances, repeatably. Our CNC Milling capabilities include full 5-axis and high-speed milling capable of hard metal, exotic, nickel alloy, and medical grade materials machining. Our emphasis is on providing the best quality machined parts to the MedTech and Aerospace markets in the most cost-efficient way; therefore, we invest in the most capable equipment.
Our CNC Turning capabilities are no less extensive, with high performing dual spindle, multi-axis machining and high-speed small diameter capability. Our Mill-Turn machines bring the significant benefits of individual CNC milling machines and lathes together for truly impressive manufacturing solutions capable of producing the most complex parts cost effectively and repeatedly. We have invested in automated robotic loading and unloading of material and parts in our CNC manufacturing cells so that we can run a light-out production operation that benefits from faster lead times and lower production costs.
Our EDM machining department provide fine-detail profile machining in a wide range of metal and carbide materials. Where high-hardness material machining or super-fine profile detail is required and conventional machining is not possible then EDM wire erosion could be the solution. We provide wire EDM machining with wire diameter down to 0.1mm allowing us to achieve smaller, finer detail in parts that many machining providers cannot.
There is an infinitely large range of parts that can be produced with the fleet of CNC machines in our Galway facility, and our engineering team will collaborate to optimise our customers design with a focus on manufacturability. We have significant capacity, highlighted in the table below, that allows us to scale our production operations to meet our customers’ requirements.
Machining Type | Machining Hours Capacity per Annum |
---|---|
Milling: 5-Axis | 70,000 |
Milling: 3-Axis | 104,000 |
Mill-Turn: 5-Axis | 10,800 |
Mill-Turn: 4-Axis | 12,000 |
Turning: 3-Axis | 4,000 |
Swiss-Turn | 12,000 |
Wire EDM | 16,000 |
Total | 228,800 |
Assembly
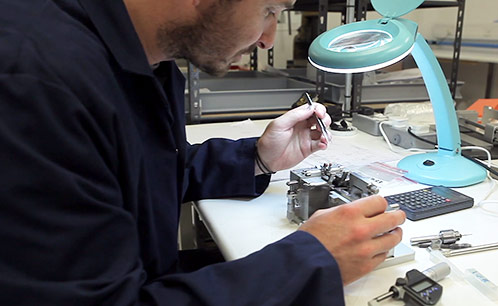
At Dawnlough we facilitate vertical integration of our clients’ product manufacturing process operations under one roof, within our own facility. In cases where clients were previously sourcing multiple components and consumables from multiple vendors, we manufacture and supply complete assemblies under a single purchase line item direct to our client’s facilities.
We accommodate transfer of product assembly processes and subassemblies that limits supply chain risk resulting in reduced lead-times, logistical planning and overall costs.
We will also assist to develop the manufacturing, assembly and testing processes themselves, putting quality assurance and quality controls in place, performing process and equipment validation, all aligned to our customers’ specific requirements.
Validation
Manufacturing process validation and equipment qualification are essential requirements of the regulated industries we serve. In accordance with ISO 13485:2016, Dawnlough has the capability to validate any process for production where resulting output cannot be verified by subsequent monitoring or measurement, therefore mitigating any risks and deficiencies at the start of the process.
CMM & VMM Inspection
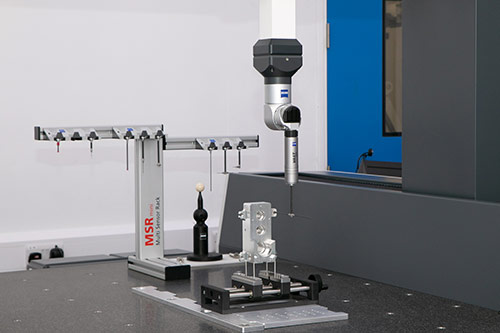
To be able to produce the best machined parts and assemblies we need to be able to measure them. Dawnlough have invested in multiple high-end Coordinate Measurement Machines (CMM) as well and Vision Measurement Machine (VMM) systems that have a high enough degree of accuracy, repeatability and functionality to inspect and examine the most challenging components with a high degree of confidence. For applications where physical contact probes may be used for complex geometries the CMM machines provide unparalleled accuracy and highly visual reporting. For applications where physical contact is not possible or required, then our highly capable vision systems can generate detailed reports that include digital images of the components.
These inspection capabilities, as well as the high calibre of qualified and experienced operators, allow us to provide a metrology service that is not found in many manufacturing solution providers. We deliver inspection solutions for our clients looking to identify root cause of failing, non-conforming product, or product demonstrating reduced functionality in the field. Included in this we can provide objective analysis reports of product drawings, detailing & tolerance strategies, and feature definition of critical & non-critical to quality features. This has enabled our clients in previous projects to actively remediate underlying or non-obvious issues with their products, as well as obtain independent inspection reports of production batch sampling.
Laser Welding & Laser Marking
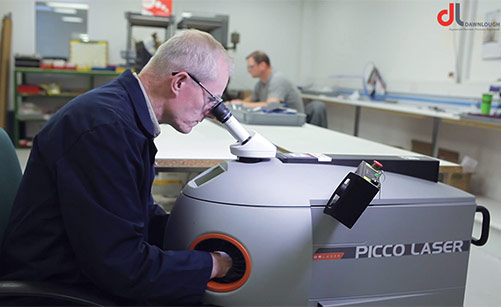
We provide high accuracy laser etching for custom and production parts to suit our clients’ products and components. Catering for low volume, purpose specific laser etching applications and for high volume serialised part numbering and barcoding of production components and assemblies. We also provide laser welding for stainless steel and alloy steel small-component applications.